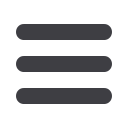
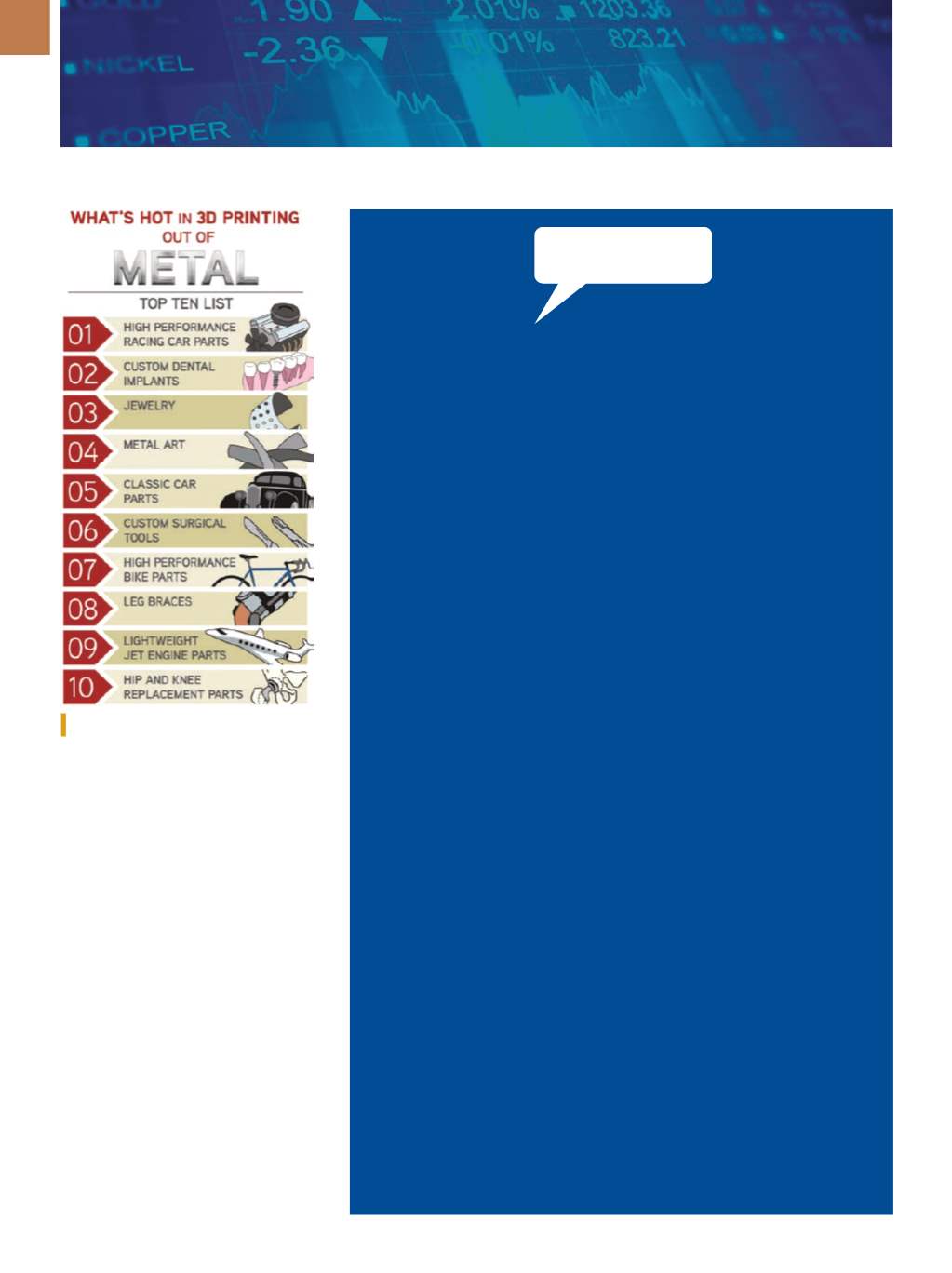
6
MARKET SPOTLIGHT
FEEDBACK
A D V A N C E D M A T E R I A L S & P R O C E S S E S | S E P T E M B E R 2 0 1 5
The articles on the early titani-
um industry (March, April, May issues)
brought back many memories. I was
released from active duty by the Army in
1953 and needed a job. I found out that
TitaniumMetals Corp. was staffing its
technical department, which sounded
exciting though I knew nothing about
titanium. TomRedden was head of
the metallurgy department and I was
the first metallurgist he hired. Tom
had come fromNational Lead and his
experience with titaniumwas as a paint
whitener. The second hire was Dwayne
Day fromBattelle. Tomdecided we
would study the Ti-Al-Mo-V system.
Dwayne was to work on sheet alloys and
my assignment was for bar.
We explored the system from Ti-8-
1-1 to Ti-1-8-8 and everything in be-
tween. This was a total joy even though
I was hampered by little knowledge of
titaniummetallurgy. We knew there was
a phase transformation somewhere
between 1800° and 1900°F and we knew
nothing of themetallography. It was Ti-
tanium101 without a professor. The only
alloys we studied that became commer-
cial were Ti-4Al-3Mo-1V and 8-1-1. Ti-4Al-
4Mo-4V was my favorite and I could heat
treat it tomore than 180 ksi, but Ti-6Al-4V
would allow no rivals then.
Tom left for a job with GE Jet En-
gines and Hal Kessler replaced him. We
now had a different agenda. Hal was con-
vinced that 6-4 could be heat treated and
that becamemy assignment. I decided
on a solution and age procedure just as I
had used on aluminum. But first I looked
at only the solution treated condition to
determine what aging would do. A tech-
Courtesy of CMU College of Engineering.
nician quenched the samples in 100°F
intervals from1400° to 1900°F. He came
tome the next day and asked if he could
use water instead of oil because he didn’t
like the smoke and oil messing up the
floor. I told him that would be fine as long
as the specimens didn’t crack. All future
heat treat specifications called for water
quenching thanks to this lab technician.
In themiddle of the heat treat
program, panic set in. Pratt &Whitney
reported that the Ti-Al-Fe alloy parts
were cracking. It was all hands on deck
because the titaniumprogramsupported
by the Air Force was about to sink. The
immediate suspect was hydrogen, so
samples were vacuumheat treated and
subjected to sustained load tests. We
didn’t know if the hydrogen could easily
be extracted andwe didn’t know if a rea-
sonable limit could be set. The program
was a total success and the limit in future
specifications became between 100 and
150 ppm. This resulted in a paper entitled
“Hydrogen in Titanium” delivered by Max
Parris who had joined us fromBattelle.
I resumed the 6-4 program and
easily achieved the 160 ksi level Hal
wanted. All titanium heat treat speci-
fications are based on our ASM paper
“The Heat Treatability of Ti-6Al-4V.”
This was reported at the Metal Show in
Philadelphia to an overflow audience. I
still appreciate Hal because he hadme
deliver the paper when he could have
claimed all the glory. Those four years
were the most fun of my career and had
a profound effect on my life.
Russell Sherman, FASM
We welcome all comments and sugges-
tions. Send letters to
frances.richards@ asminternational.org.
THE JOY OF TITANIUM
In conjunction with the first Na-
tional Maker Faire and the White House
Week of Making held in Washington in
June, Carnegie Mellon University (CMU)
experts created a Top 10 list for 3Dmetal
printing. “We havemany faculty working
to improve 3D printing of metals, from
powder properties and manufactur-
ing outcomes to cost and public policy
issues,” says Jack Beuth, professor of
mechanical engineering. “Much of this
learning is being applied to jet engine
parts, but the technology is already be-
ginning to trickle down to a wide variety
of custom metal components and re-
placement parts.” Beuth’s research fo-
cuses on mapping outcomes of various
3D printing methods to make the pro-
cess faster and cheaper when applied to
metals.
engineering.cmu.edu.