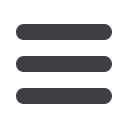

New design aims toward crash-free cars
Volvo, Sweden, hopes
to achieve a goal of zero
vehicle fatalities or seri-
ous injuries in their mod-
els by 2020. The new
scalable product architec-
ture (SPA) significantly
improves protection in
worst-case scenarios and
creates innovative fea-
tures to help drivers avoid
accidents. The safety cage
in the original XC90 con-
tained 7% hot-formed
boron steel, while the new
version features more
than 40% hot-formed steel, which improves strength without adding mass or weight. Cars
built on the new SPA have smart belt pre-tension systems that help keep occupants in the
vehicle before and during collisions. For example, a rearward-facing radar detects rear
impact, so safety belts tighten in advance to keep occupants in place. Camera, radar, and
sensor technologies are extended to detect more objects around the car and offer support
at higher speeds and in more situations, such as at intersections. The new features also
auto brake for large animals and pedestrians when driving in the dark.
www.volvocars.com.
New alloys for use in aerospace components
IBC Engineered Materials Corp., Wilmington, Mass., is working directly with Lock-
heed Martin’s F-35 electro-optical targeting system (EOTS) engineering, design, and
quality teams in Orlando to develop components to demonstrate the technical and com-
mercial viability of their Beralcast alloys as alternatives to parts made from beryllium-alu-
minum alloys. Several advanced prototype castings are being used to evaluate the new
alloys and castings for critical structural and sub-system aerospace components. Beral-
cast alloys can be used in virtually any high performance application requiring complex,
lightweight, and high-stiffness parts. The new alloys can be substituted for aluminum,
magnesium, titanium, and metal matrix composites, as well as pure beryllium or powder
metallurgy beryllium-aluminum. Beralcast’s principal alloys are more than three times
stiffer than aluminum with 22% less weight and can be precision-cast for simple and com-
plex 3D stability.
www.ibcadvancedalloys.com.
Lowering titanium’s cost for lightweight products
A novel method for extracting titanium significantly reduces the energy required to
separate it from its tightly bound companion, oxygen. Zhigang Zak Fang, professor of
metallurgical engineering at the University of Utah, Salt Lake City, and colleagues note
that while titanium is the fourth most common metal in the Earth’s crust, the high-en-
ergy, high-cost method used to extract it prevents its use in
broader applications.
The most common technique, called the Kroll process, used
to extract the metal from titanium oxide was invented in the
1930s and has undergone slight improvements. The method
requires temperatures above 1800°F and is expensive. Fang’s
team was able to eliminate the energy-intensive steps of the
Kroll process. In the lab, they successfully tested a new series
of reactions for isolating titanium that halves the temperature
requirements of the conventional method and consumes 60%
news
industry
briefs
R
esearch led by
University of
Nebraska-Lincoln
found that
using a small amount of graphene
oxide as a template improves
carbon nanomaterials, promising to
improve composite materials. The
graphene oxide nanoparticles are
incorporated as a template to
guide the formation and orientation
of continuous carbon nanofibers. A
group led by chemist SonBinh
Nguyen of
Northwestern
University,
Evanston, Ill.,
synthesized the graphene oxide,
and the resulting carbon nanofiber
structure has an orientation similar
to fibers with enhanced properties.
These graphene-based nanofibers
are now being tested for enhanced
properties and to improve the
technique.
www.unl.edu,
www.northwestern.edu.
REFORM
(resource-efficient
factory of recyclable manufacturing
composite) is a project funded by
the
European Commission
and
focuses on the manufacture of
composites to develop cleaner,
more efficient technologies for
composites manufacturing. These
composites are produced with a
polymer base and reinforced with
fiber, allowing fabrication of lighter
components that maintain or
improve mechanical properties.
The methods considered are
rolling, machining (cutting and
edge finishing), assembly, and
recycling.
Tecnalia,
Spain, is
working alongside 13 partners and
is gearing its work toward
machining composite materials,
using waterjet as well as
conventional cutting.
http://reform.eu.com,
www.tecnalia.com/en.M
ETALS
P
OLYMERS
C
ERAMICS
ADVANCED MATERIALS & PROCESSES •
FEBRUARY 2014
6
The XC90 safety cage is built using the new scalable product
architecture and features more than 40% hot-formed steel, which
translates into significantly improved strength without adding
mass or weight.
Walter Voit, assistant professor of materials science and engineering and
mechanical engineering at the
University of Texas,
Dallas, was awarded
$1 million to create medical devices with greater control of prosthetics in
wounded soldiers. He created shape memory polymers that can respond
to the body’s environment and become less rigid when implanted in the
body. These polymers are implanted when they are rigid and then flex
toward the stiffness of the tissue. The medical devices should survive
implantation in the body for more than one year. For more information:
Walter Voit, 972/883-5788,
walter.voit@utdallas.edu,
www.utdallas.edu.