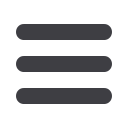

A D V A N C E D
M A T E R I A L S
&
P R O C E S S E S |
S E P T E M B E R
2 0 1 5
1 5
PROCESS TECHNOLOGY
Switzerland, will cooperate in North
America, Europe, and Asia to provide
integrated casting and machining solu-
tions to automotive, industrial, and
commercial customers. Linamar man-
ufactures precision forged and ma-
chined metallic components, modules,
and systems for engine, transmission,
and driveline systems. GF Automotive
manufactures lightweight cast compo-
nents and systems for automotive and
industrial applications. The companies
will build a new light metal foundry
in the southeastern U.S. to produce
high-pressure die castings for power-
train, driveline, and structural compo-
nents.
linamar.com.
NEW TECHNIQUE HOLDS
PROMISE FOR URANIUM
EXTRACTION
A research team at Murdoch Uni-
versity, Australia, recently discovered
a technique to extract uranium from
brannerite, a mineral often considered
a waste product. Researchers say the
knowledge could produce results within
two to three years. Ph.D. candidate Rorie
Gilligan says the discovery started from
simple curiosity about where uranium
volume was lost in extraction, which
led him to the often overlooked bran-
nerite. “The assumption has been that
brannerite can’t be processed,” says Gil-
ligan. “I found a number of papers from
the 1950s and 60s exploring branner-
ite extraction, which gave us a starting
point.”
The research fit into an ongo-
ing project headed by Aleks Nikoloski
aimed at understanding uranium ex-
traction. Over the past three years, Gil-
ligan has been running trials on both
pure brannerite specimens and mixed
mineral conditions likely to occur in
natural deposits. Conventional wisdom
suggests increasing the acid or alkaline
environment will increase the rate of
leaching for hard-to-extract minerals,
but researchers found this wasn’t the
case with brannerite. “At first I couldn’t
believe the results. We were getting an
extraction rate of 80-90% for a mineral
that was supposed to be refractory,”
says Nikoloski. The project is now at-
tracting interest from uranium-mining
countries worldwide, including Austra-
lia, China, Russia, and Canada.
www. murdoch.edu.au.
LIFT’s first project aims to decrease the wall thicknesses of ductile iron cast parts
by up to half.
LIFT EXPLORES IRON ALLOYS
IN THIN-WALL CASTINGS
Casting parts from molten iron is a
standard process that has been recently
transformed by technological advances.
LIFT (Lightweight Innovations for Tomor-
row), Detroit, will investigate innovations
in melt processing as its first technology
acceleration project. Grede, Southfield,
Mich., and Michigan Technological Uni-
versity, Houghton, will lead the project,
which focuses on reducing the amount
of metal used to make automotive trans-
mission differential cases, similar to core
product designs provided by Grede and
Eaton. By integrating and implementing
improved manufacturing methods with
different alloys, the wall thicknesses
of ductile iron cast parts could be de-
creased by up to 50%, achieving 30-50%
weight savings in various parts.
LIFT, operated by the American
Lightweight Materials Manufacturing In-
novation Institute (ALMMII), is one of the
founding institutes in the National Net-
work for Manufacturing Innovation. ASM
is part of the LIFT consortium and will
assist with educationworkforce develop-
ment initiatives.
www.lift.technology.
NEW LIGHT METAL FOUNDRY
ANNOUNCED
Linamar Corp., Ontario, and GF
Automotive (part of Georg Fischer AG),
Brannerite. Courtesy of Rob Lavinsky/
irocks.com.