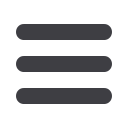

A D V A N C E D
M A T E R I A L S
&
P R O C E S S E S |
S E P T E M B E R
2 0 1 5
1 7
SURFACE ENGINEERING
NEW COMPOSITE WITHSTANDS
CORROSION AT HIGH
MECHANICAL STRESS
Materials researchers at the INM–
Leibniz Institute for New Materials, Ger-
many, developed a composite material
that prevents metal corrosion in an en-
vironmentally friendly way, even under
extreme conditions. “This patented com-
positeexhibits itsactionby sprayapplica-
tion,” explains Carsten Becker-Willinger,
head of the Nanomers Program Division.
“The key is the structuring of this layer—
the protective particles arrange them-
selves like roof tiles. As in a wall, several
layers of particles are placed on top of
each other in an offset arrangement; the
result is a self-organized, highly struc-
tured barrier.” The protective layer is just
a few micrometers thick and prevents
penetration by gases and electrolytes.
It provides protection against corrosion
caused by aggressive aqueous solutions,
including salt solutions such as salt spray
on roads and seawater, or aqueous acids
such as acid rain.
After thermal curing, the compos-
ite adheres to the metal substrate and
is both abrasion-stable and impact-
resistant. The composite can be applied
by spraying or other commonly used
wet chemistry processes and cures at
150°-200°C. It is suitable for steels, met-
al alloys, and metals such as aluminum,
magnesium, and copper, and can be
used to coat any shape of plates, pipes,
gear wheels, tools, or machine parts.
For more information: Carsten Becker-
Willinger, +49.068.1930.0196,
carsten. becker-willinger@leibniz-inm.de, tinyurl. com/ohhw6wy.NEW LASER METHOD APPLIES
DIAMOND-LIKE COATINGS
Coating engine components with
hard carbon reduces friction to almost
zero—a development that could save
billions of liters of fuel worldwide ev-
ery year. Now researchers developed a
new laser method to apply the coating
on the production line. Scientists al-
ready know how to coat components
with diamond-like carbon to minimize
friction. But researchers developed a
laser arc method with which layers of
carbon almost as hard as diamond can
be applied on an industrial scale at high
A new composite material prevents metal corrosion.
BRIEF
A nanoLED SEM image by
Eindhoven University of Technology
(TU/e),
the
Netherlands, won a competition held by
Oxford Instruments Plasma Tech-
nology,
UK. Submitted by Ph.D. candidate Victor Dolores-Calzadilla from the
Photonic Integration Group at TU/e, the SEM image titled “Integrated nan-
oLED for Photonic Circuits” was achieved using a combination of three Oxford
plasma processing tools and demonstrates plasma etch and deposition
technology.
oxford-instruments.com/SEM-2015.coating rates and with high thickness-
es. By applying carbon coatings to en-
gine components such as piston rings
and pins, fuel consumption can be re-
duced. “Systematic application of our
new method could save more than 100
billion liters of fuel each year over the
next 10 years,” says Andreas Leson from
the Fraunhofer Institute for Material
and Beam Technology IWS, Dresden.
Carbon-basedcoatings arealreadyused
in volume production. But the team
succeeded in producing hydrogen-free
ta-C coatings on an industrial scale at a
consistent level of quality. These tetra-
hedral amorphous carbon coatings
are significantly harder and thus more
resistant to wear than conventional
diamond-like coatings.
The laser arc method generates
an arc between an anode and a cath-
ode (the carbon) in a vacuum. The arc
is initiated by a laser pulse on the car-
bon target. This produces a plasma
consisting of carbon ions, which is de-
posited as a coating on the workpiece
in the vacuum. To run this process on an
industrial scale, a pulsed laser is verti-
cally scanned across a rotating graphite
cylinder as a means of controlling the
arc. The cylinder is converted evenly
into plasma thanks to the scanning mo-
tion and rotation. To ensure a consis-
tently smooth coating, a magnetic field
guides the plasma and filters out any
particles of dirt. The laser arc method
can be used to deposit very thick ta-C
coatings of up to 20
μ
m at high coating
rates.
For more information: Andreas Le-
son, +49.351. 83391.3317,
nanofair.com.