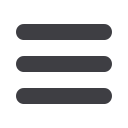
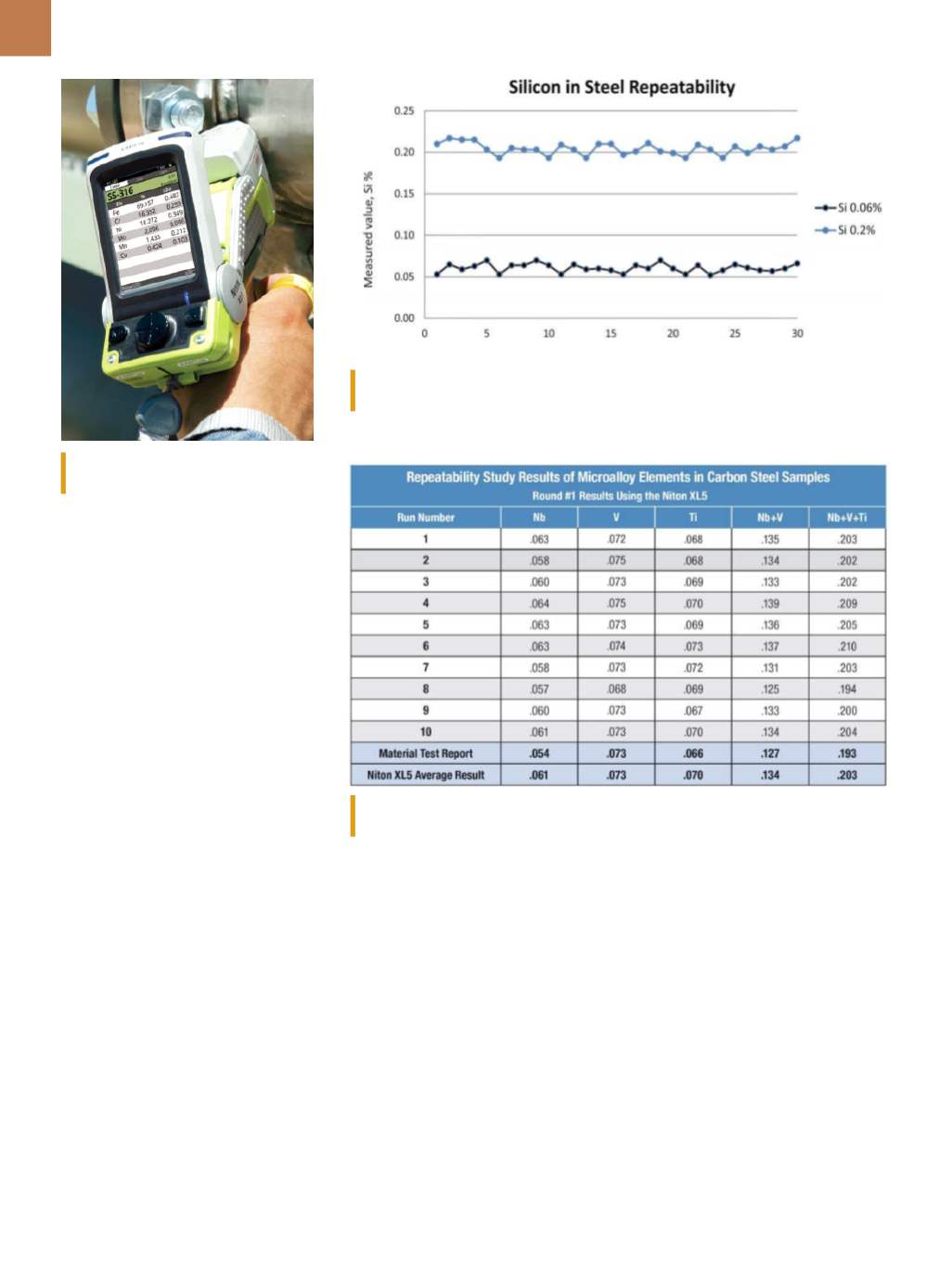
A D V A N C E D M A T E R I A L S & P R O C E S S E S | S E P T E M B E R 2 0 1 6
2 2
zation field has seen XRF technology
evolve and even match OES in terms of
performance and reliability. XRF is now
incorporated into much smaller instru-
mentation than ever before, allowing
easier access to hard-to-reach areas
such as corner welds, inside vessels
and exchangers. Inherent to its smaller,
lightweight design, it can also help
reduce operator fatigue.
How is XRF technology used in plants
and refineries?
The greatest advantage of XRF
technology is user productivity. Mod-
ern XRF equipment can take a mea-
surement in a few seconds with little
sample preparation and produce real-
time results that allow users to make
immediate decisions. XRF analysis is
also nondestructive. These are major
advantages compared to lab testing,
which often requires removing a seg-
ment of the sample and sending it to an
offsite lab for results. Another advan-
tage is ease of use. Modern XRF ana-
lyzers are smaller, faster, and smarter
instruments than previous generations.
This allows users without extensive
materials analysis training to measure
the elemental composition of a metal
pipe or component onsite.
What are you seeing with regard to
standards and legal requirements?
In the United States, we are see-
ing increased pressure from regulatory
groups like the EPA (Environmental
Protection Agency) and OSHA (Occu-
pational Safety and Health Adminis-
tration) demanding that asset holders
know the composition of materials they
have in place. Because portable ana-
lyzers are easier to use than earlier ver-
sions, employees at industrial sites are
beginning to conduct materials analysis
themselves. By enabling onsite workers
to conduct measurements without hir-
ing a third-party contractor or sending
samples to a lab, industrial sites can
prove to regulators that they have a
program in place to monitor and man-
age corrosion. As the oil refining and
petrochemical industries continue to
require more inspection and data col-
lection, we expect that use of portable
XRF metal analyzers will become even
more common.
~AM&P
For more information:
Brian Wilson is
business development manager, energy
markets,portableanalyticalinstruments,
Thermo Fisher Scientific, 2 Radcliff Rd.,
Tewksbury, MA 01876, 713.380.1287,
brian.k.wilson@thermofisher.com, ther-
mofisher.com/portableid.
Elemental content of steel piping inspec-
tion with the Niton XL5 XRF analyzer.
Low- and high-standard silicon in carbon steel measurement results using the
Niton XL5 XRF analyzer.
Microalloy element measurements of carbon steel samples using the Niton XL5 XRF analyzer
agree with laboratory test results.
Repeat measurements