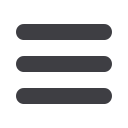
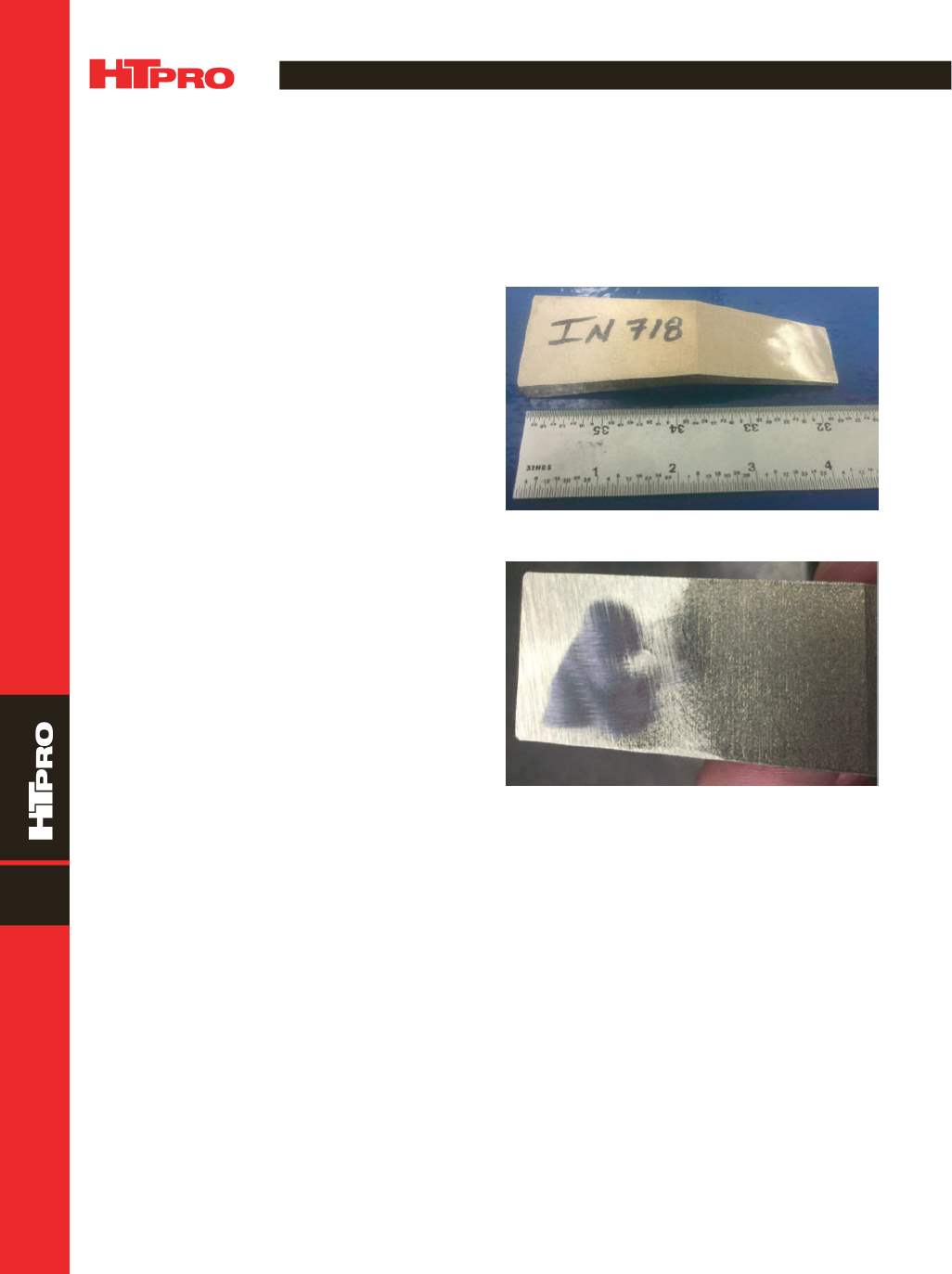
FEATURE
A D V A N C E D M A T E R I A L S & P R O C E S S E S | S E P T E M B E R 2 0 1 6
4 6
14
A
dditive manufacturing (AM) is becoming an increas-
ingly popular production method for making metal
parts with complex geometries. AM offers a solu-
tion for producing components with geometrical features
that are difficult to create through traditional casting, forg-
ing, forming, and machining methods. One example is a
3D-printed Inconel 718 component used in fluid flowcontrol.
The component has many small, intricate internal passage-
ways that control andmoderate the flowof an abrasive fluid.
The small holes, internal twisting passageways, and open-
ings would be very difficult to machine from a solid piece of
material. Traditionally, investment casting would be used to
produce a near-net-shape part, but some machining is still
required to add intricate features. AM offers an alternative
production method to near-net-shape casting, post machin-
ing, and grinding.
BORONIZING FOR IMPROVED
WEAR RESISTANCE
Erosion wear of flow control unit internal surfaces
from abrasive fluid flow affects flow rates, which in turn af-
fects the proper function of the unit. Increasing wear resis-
tance is therefore necessary to improve the unit’s service
life. Boronizing is a proven method for reducing wear and
erosion of metal surfaces on parts produced using tradi-
tional manufacturing methods. However, it was unknown
how an AM part would respond to boronizing. To explore
this idea, Bluewater Thermal Solutions investigated what
effects, if any, AM Inconel 718 material had on its boroniz-
ing process.
Boriding tests were conducted on a sample of
3D-printed Inconel 718, which represented a portion of a
3D-printed component (Fig. 1). The investigation was per-
formed to determine if a 3D-printed surface has a negative
effect on boronizing results compared with typical results
for boronized conventional wrought Inconel 718 material.
Because the as-printed surface was fairly rough, the
smaller end of the sample was ground using a belt sander
to remove some as-printed surface material (Fig. 2). This
enabled a determination to be made regarding whether
surface roughness or surface defects from the printing pro-
cess negatively affect boride layer formation.
The test sample was packed in Bluewater’s propri-
etary boronizing powder inside a sealed retort and pro-
cessed in a furnace at a temperature of 1475
°
F for 8 hours to
BORONIZING ADDITIVELY MANUFACTURED INCONEL 718
Boronizing 3D-printed Inconel 718 produces results similar to those obtained for wrought 718.
Craig Zimmerman,*
Bluewater Thermal Solutions, Chicago
prevent laves phase or grain boundary carbide precipitation
during simultaneous boronizing and aging.
TEST RESULTS
Figure 3 shows the boronized as-printed and ground
surfaces. The ground surface remained smoother than the
unground surface, and it was difficult to visually identi-
fy the ground surface. Sectioning the sample provided a
cross section containing both the boronized ground and
unground surfaces. The cross section was mounted and
examined metallographically to determine boride layer
depth. Vickers microindentation hardness (50 g load) of
the boride layer was measured in three locations. Core
hardness (HRC) was measured in four locations on the
cross section in the mount. No difference was observed
between the ground and unground sides of the part. Both
sides had a boride layer with similar appearance (Fig. 4).
Figure 5 shows the core microstructures.
Fig. 1 —
Test segment of 3D-printed Inconel 718.
Fig. 2 —
Ground surface on small end of test segment.
*Member of ASM International