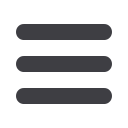

A D V A N C E D
M A T E R I A L S
&
P R O C E S S E S |
M A Y
2 0 1 6
3 7
CONFERENCE HIGHLIGHTS
ADVANCEMENTS IN TITANIUM
TECHNOLOGY
Developments in titanium technology and opportunities for increased use in several
markets were highlighted at the 13th World Conference on Titanium (Ti-2015).
Vasisht Venkatesh, Pratt & Whitney, East Hartford, Conn.
Rodney Boyer (retired), Boeing, and RBTi Consulting, Bellevue, Wash.
Many of these developments were
discussed at the 13th World Conference
on Titanium, held during August 2015 in
San Diego, Calif. This article highlights
some of the major advancements pre-
sented at the conference.
NEW ALLOY DEVELOPMENT
Conventional titanium alloys are
typically limited to a maximum tem-
perature of roughly 500°-550°C due to
poor oxidation resistance. In addition,
severe grain growth in single-phase
titanium alloys at elevated tempera-
tures degrades its mechanical prop-
erties. During a few of the conference
sessions, recent titanium develop-
ments were presented to provide an
overview of the industry. For example,
Kobe Steel Ltd., Japan, developed sev-
eral titanium alloys over the past two
decades including:
•
Ti-0.4Ni-0.015Pd-0.025Ru-0.14Cr
(AKOT), a corrosion-resistant alloy
T
he aerospace sector consumes
more than 70% of all titanium
produced in the U.S., but major
opportunities exist for increased use
in the automotive and biomedical sec-
tors, as well as other industrial sectors.
This is being driven by factors such as
new process development to lower
manufacturing costs, enhancing per-
formance of existing and new titanium
alloys to meet new application require-
ments, and development of computa-
tional models to both reduce new alloy
development cycle times and acceler-
ate new process qualification times at
reduced cost.
The aerospace industry is contin-
ually looking for titanium products for
next-generation airframes and engines
to meet stringent fuel efficiency stan-
dards and cost pressures associated
with large orders for new aircraft
such as the B787, B777X, B737MAX,
A320NEO, A350XWB, and A380 (Fig. 1).
Thus, some of the latest developments
focus on growing titanium use through
innovation in key capabilities and
reduced final component costs. Exam-
ples include development and qualifi-
cation of a third-generation forgeable
γ
-TiAl for low-pressure turbine blades
in the Pratt & Whitney PW1000G engine
and evaluation of new
α
+
β
alloys for
superplastically formed nacelle compo-
nents in next-generation airframes and
engines.
Fig. 1 —
Increased titanium use in aircraft over the past several decades. Bubble size indicates
aircraft passenger capacity
[1]
.